Explosion-proof lamps are used in hazardous locations where flammable gases and dust are present. They can prevent arcs, sparks, and high temperatures inside the lamp from igniting flammable gas and dust in the surrounding environment, thereby reaching the explosion-proof requirements. Also known as explosion-proof lighting, explosion-proof lighting. Different flammable gas mixture environments have different requirements for the explosion-proof grade and explosion-proof form of explosion-proof lamps. Specific reference GB3836, IEC60079.
I. Outline
With the rapid development of petroleum, chemical, mining and other industries, lighting fixtures are increasingly used in production, warehousing, and rescue, with more and more varieties. How to prevent accidental explosion of lighting fixtures has become a very important issue in explosive gas hazardous locations. As the lighting fixtures inevitably generate sparks or form hot surfaces when they work, once they meet the explosive gas mixture at the production or rescue site, it will lead to an explosion accident that will directly endanger the lives of national property and citizens. Therefore, as the most widely used lighting fixture, its explosion-proof technology has long attracted people's attention and great attention. Use aluminum alloy shell, surface spray; lighting, emergency dual-use; Built-in maintenance-free nickel-cadmium battery pack, automatic charging under normal power supply, accident power failure or power failure to automatically light up the emergency light; steel pipe wiring; emergency dedicated lamp normal The lighting and emergency lighting are independent; the lighting emergency dual-purpose lamp, normal lighting and emergency lighting share one lamp body and the light source is independent.
Second, the scope of application
1.Applicable to hazardous areas in Zone 1 and Zone 2 in explosive gas atmospheres;
2. Suitable for IIA, IIB, IIC explosive gas environment;
3. Suitable for flammable dust environment 20 area, 21 area, 22 area;
4 applies to the temperature group T1-T6 ring
Third, performance characteristics
1, with T8LED lamp, light source energy efficient, than the T8 fluorescent lamp energy saving more than 50%.
2, through a unique light design, precise control of the LED light source light and light angle, to avoid light pollution and the use of invalid light; soft light, no glare, will not cause operator fatigue, improve work efficiency.
3, the shell is made of light aluminum alloy die-casting, and the surface is treated with high pressure electrostatic spray.
4. There are wiring chambers inside the lamps and there are special wiring terminals. The user can directly enter the line during installation, and no additional junction box is required for easy installation.
5, when replacing the lamp, just fold down the end cover, you can directly replace the lamp.
6, according to customer requirements matching international famous brand T5 fluorescent tubes, high luminous efficiency, more in line with the actual lighting environment, compared with T8 fluorescent tubes save about 30%.
7, can be equipped with emergency equipment according to user requirements, built-in light body light weight, when the outside world power, the light automatically switches the emergency lighting state.
Four, lamp type classification
1, classification
Explosion-proof light is generally classified according to the selected light source, explosion-proof structure type, and usage mode. According to the light source classification, there are explosion-proof incandescent lamp, explosion-proof high-pressure mercury lamp, explosion-proof low-voltage fluorescent lamp, mixed light source lamp, etc.; according to the explosion-proof structure type, there are explosion-proof lamps, increased safety lamps, composite lamps, etc.; Explosion-proof lamps and portable explosion-proof lamps.
2, type
According to the explosion-proof type, it can be divided into 5 types: flameproof, increased safety, positive pressure, non-sparking and dust explosion-proof. It can also be combined by other explosion-proof types and the above-mentioned various explosion-proof types or composite type and special type. .
3, explosion-proof type d
The components of the device that may ignite the explosive gas mixture are all enclosed within a housing that is capable of withstanding any interface or structural gap through the housing. The flammable mixture that has penetrated into the interior of the device explodes without damage and ensures internal The flame gas reduces energy when propagating through the gap and is not enough to detonate the shell gas.
4, increased safety e
Electrical equipment that does not produce arcs or sparks under normal operating conditions will take additional measures to increase its safety and prevent explosions of the possibility of dangerous temperatures, arcs and sparks in its internal and external components. Protection measures to improve equipment reliability and safety performance.
5, positive pressure type p
By keeping the pressure of the protective gas inside the device enclosure higher than the surrounding explosion-proof ambient pressure to a safe electrical device, a static positive pressure is maintained inside the system or a continuous flow of air or inert gas is maintained to restrict entry of the flammable mixture into the interior of the enclosure. The flammable gas that enters the enclosure when the device is in a non-positive pressure state is taken away to prevent the formation of a flammable mixture in the enclosure.
6, this placement I
All circuits inside the equipment are intrinsically safe circuits of the explosion-proof gas atmosphere that are not specified by any spark or any effect produced under standard conditions (including normal operation and specified fault conditions).
7, sealing type m
Explosive sparks, arcs, or dangerous temperature electrical components that may ignite the explosive mixture will be encapsulated in the encapsulant (composite) so that it cannot ignite the surrounding explosive mixture. Enclosure measures are used to prevent electrical components. Short-circuiting, solidification of electrical insulation prevents sparks on the circuit and the ignition of arcs and hazardous temperatures, prevents intrusion of explosive mixtures, and controls surface temperatures under normal and fault conditions.
8, oily o
The entire equipment or components of the equipment are invaded in the oil I protection fluid l so that it cannot ignite the explosion-proof gas environment above the oil surface or outside the housing.
9, sand filling q
The shell is filled with sand or other powder material of specified characteristics so that, under the specified conditions of use, arcs or high temperatures generated in the shell cannot ignite the type of electrical equipment protection of the surrounding explosive gas atmosphere.
10, airtight type h
This type of explosion-proof equipment uses airtight enclosures. That is, the explosive gas mixture in the environment cannot invade the inside of the device housing. The airtight enclosure is sealed by melting, squeezing or gluing. This enclosure is mostly non-detachable to ensure permanent tightness.
11, protection class
Classified according to the protection class of the enclosure: In order to protect the dust, solid foreign matter and water from entering the lamp cavity and touching or accumulating on the live parts to cause flashover, short circuit or damage to the electrical insulation, etc., there are a variety of enclosure protection methods to protect the electrical Insulation effect. The characteristic letter "IP" followed by two digits is used to characterize its enclosure protection level. The first number indicates the protection against humans, solid objects or dust. Divided into 0-6 levels. Explosion-proof lamps are sealed lamps. Their dust-proof capacity is at least 4 levels. The second number indicates the protection against water and is classified into 0-8.
12, support surface material
According to the lighting design of the support surface material classification: Indoor explosion-proof lighting may be installed on many common surfaces of combustible materials, such as wooden walls and ceilings, which do not allow explosion-proof lighting installation surface temperature exceeds the safety value. According to whether explosion-proof lamps can be installed directly on the surface of ordinary combustible materials, they can be classified into two categories. One category is lamps that are only suitable for installation on non-combustible surfaces; the other category is lamps that are suitable for direct installation on the surface of common combustible materials, and are marked with symbols. In addition, according to the form of installation can be divided into fixed, portable, portable.
14, principle
The explosion-proof type principle According to the explosion-proof concept and fire type of the European standard EN13463-1:2002 "Non-electrical equipment for explosive atmospheres Part 1: Basic methods and requirements", the flameproof type adopts measures to allow internal explosion and prevent flame propagation. An explosion-proof type is the most commonly used explosion-proof type. Since the explosion-proof type lamp housing is generally made of a metal material, the heat dissipation is good, the strength of the housing is high and the durability is good, and it is very popular with users. Moreover, many increased safety explosion-proof lighting components, such as lamp holders, interlock switches, etc., are also flameproof structures. An electrical device with a flameproof enclosure is called a flameproof electrical device. If the explosive gas mixture enters the flameproof enclosure and is ignited, the flameproof enclosure can withstand the explosive pressure of the internal explosive gas mixture and prevent the internal explosion from propagating to the explosive mixture around the enclosure. This is a kind of clearance explosion-proof principle, that is, a structure designed by using the metal gap to prevent the propagation of the explosion flame and cool down the temperature of the explosion product, to achieve flame extinction and temperature reduction, and to suppress the expansion of the explosion principle.
15, design
In the structural design of explosion-proof lighting fixtures, manufacturers often focus on the design and strength of the flameproof enclosure, but often overlook the fasteners, lead-in devices, transparent parts, suspension devices, signs, etc. that are integral with the enclosure. Design of other devices. Next, according to the requirements of GB3838.2-2000 “Electrical Equipment for Explosive Gas Environments Part 1: Flameproof Type “dâ€â€, some issues needing attention in the structural design are analyzed:
16, shell fasteners
There are two types of flameproof enclosures that are fastened with bolts: flat and spigot. For flat structures, the bolts not only perform tightening operations, but also ensure the plane clearance. For the stop structure, when the flameproof surface only considers the cylinder part, the bolt only plays a fastening role; when the flameproof surface needs to consider the cylinder plus the plane, the bolt not only acts as a fastening operation, but also plays a role in ensuring the clearance of the plane part. When tapping directly on the shell, attention must be paid to the following: Screw holes of fasteners should not pass through the flameproof enclosure as much as possible, and 3mm or more of the margin should be left at the bottom of the screw hole when passing through the shell; light alloy materials such as aluminum alloy should be used to separate them. When blasting the shell, due to the low strength of the aluminum alloy, when using the screws to fasten the explosion-proof shell that is often opened (such as when the replacement light source needs to be opened), the threads should not be tapped directly on the aluminum alloy shell; The internal and external thread steel sleeves are used to increase the screw hole strength and prevent failure due to thread rotting; it is not necessary for the user to open the replacement light source or maintenance, and the bolts already installed at the factory can be tapped directly on the shell. Screw hole, but can not use fine thread, try to use coarse thread, and there is enough engagement to meet the fastening requirements. In short, in the design of shell fasteners, it should first distinguish its role in the flameproof enclosure, is only to play a role in fastening, or both to play at the same time to ensure the role of plane clearance, and then determine the maximum axial bolt Use suitable bolts for the load.
17, introduction method
The introduction of cables and wires can be connected as follows:
a) indirect introduction, connection by junction box or plug-in device;
b) Directly introduce the connection of cables and wires directly to the main housing. It is worth noting that the seal can burn or explode directly when the aging or pressure is not tight.
Therefore, explosion-proof lamps classified as Class IIC are not suitable for generating dangerous sparks, arcs, or dangerous temperatures during normal operation and the enclosure volume is greater than 2000 cm3 or GB3836.1 "Electrical Equipment for Explosive Gas Environments Part 1: General Requirements". The elastic sealing ring presses the direct introduction method. Although GB3836.2 does not describe this, GB3836.15-2000 “Electrical Equipment for Explosive Gas Environments Part 15: Electrical Installation in Hazardous Locations (Excluding Coal Mines)†regulates this. Through the cable introduced into the fixture through the introduction device, from the installation to the use of the entire process, if possible to be subject to tension, the introduction of the device on the compression nut or close to the introduction of the device inside the lamp to increase the cable pull-out pressure plate to prevent the force transmitted to the terminal block Prevents possible movement of the cable and prevents contact or failure of the electrical connection. Lamps may need to be provided with more than one lead-in device at design time to facilitate different installation requirements of the user. All sealing devices shall be installed at the time of shipment from the factory. The structure of the sealing device must be suitable for explosion protection. Alternatively, only one lead-in device is installed, and the remaining holes (after removal of the lead-in device) are replaced by plugs suitable for explosion protection. In this way, the failure of the flameproof enclosure will not be caused by the unintended plugging of the lead-in device.
18, transparent parts installation
Explosion-proof lighting is inseparable from the transparent parts, and the transparent part is the lowest strength part of the shell parts. Therefore, whether the transparent parts are installed directly affects the safety performance of the explosion-proof lamps.
The following analysis of three commonly used transparent parts installation method: a) directly sealed in the shell, forming a whole with the shell. This method is simple, practical and widely used. Sealing materials should be selected from rubber parts that are resistant to temperature and oil, or adhesives such as epoxy resin can be used to seal the transparent parts in the housing and press them tightly.
b) Secure the transparent member directly in the housing with or without a gasket. The flatness of the bonding surface of the transparent member is not required when the gasket is not used, and is generally suitable for a small flat glass and the glass bonding portion is polished at the same time. Otherwise, the glass is not uniformly subjected to stress and is easily broken.
c) Sealed or glued to a frame that is secured within the housing so that the transparent member can be replaced as a whole. This kind of structure is rarely used in luminaires. In some large devices that require frequent replacement of transparent parts, the transparent parts and the frame are replaced as a single unit.
The sealing of the transparent member and the frame can refer to the type of a). In terms of structure, the force (inner explosion) received by the transparent member should be directly transmitted to the metal shell as far as possible, and it is not suitable to pass the transparent platen and/or screws to the metal shell. At the same time, the transparent member is installed. Can not be subjected to stress, so as to ensure reliable combination of transparent parts and shell.
Fifth, selection
1, select the model
The selection, installation, use and maintenance of explosion-proof lighting fixtures are all indispensable links for long-term safe, reliable and efficient operation of explosion-proof lighting fixtures and must be given full attention.
(1) The selection personnel must understand the basic working principle of the explosion-proof lighting and be familiar with the explosion-proof mark.
(2) Accurately select the explosion-proof category, type, grade and temperature group of the lighting according to the level of the explosive hazardous area.
(3) Understand the use of environmental conditions and work requirements, and reasonably select explosion-proof lamps with various functions. For example: The explosion-proof lamps and lanterns used outdoors have a degree of protection of at least IP43. In locations where color is required to be identified, high-pressure mercury lamps and high-pressure sodium lamps may not be selected as explosion-proof lamps because the color rendering of the two light sources is poor.
(4) Read the product instruction manual in detail to understand the product performance, precautions, and product limitations, and to understand the contents of all the product's marks. If the explosion-proof certificate number is followed by an "x" symbol, it indicates that the lamp has a specific applicable location. The product instruction manual and the nameplate should be consulted to clarify the applicable site requirements.
2, light source selection
(1) Although incandescent lamps are still used more, they are being gradually replaced by other light sources due to their low luminous efficiency and short lifetime. Among them, single-plug non-starter fluorescent lamps, self-ballasted high-pressure mercury lamps, and high-pressure sodium lamps are widely used.
(2) Single-plug non-starter fluorescent lamp is a kind of cold-cathode gas discharge lamp. The principle of luminescence is to use the discharge between the electrodes to make the mercury atoms generate ultraviolet radiation, thereby igniting the fluorescent material on the inner wall of the lamp tube. This fluorescent lamp has a high luminous efficiency (about 3 times that of incandescent lamps) and has a long service life. It does not require a starter for starting (usually a conductive layer on the lamp tube wall, called the glow layer, the fluorescent lamp Rely on it to complete; when the lamp ruptures, the glow layer is also destroyed, the lamp is extinguished), and the cathode temperature is low (about 200°C or so), which is a safe and practical light source, and is very suitable for making increased safety lighting fixtures. .
(3) Self-ballasted high-pressure mercury lamp is a hybrid light source lamp that utilizes high-pressure mercury vapor discharge, and incandescent body and fluorescent substances emit light. It has the advantages of high brightness, simple structure, fast starting speed and so on. The disadvantages of external ballasts need to be changed in the prior art high-pressure mercury lamps. The use of tungsten filaments acts as a current limiter and also improves light color. The disadvantage is that the lifetime is shortened compared to ordinary fluorescent high-pressure mercury lamps. The high-pressure sodium lamp is a high-pressure sodium vapor discharge lamp, which has the advantages of high luminous efficiency, low power consumption, strong fogging ability, long service life, and the like.
3, structure type
Explosion-proof lamp explosion-proof structure type, according to the regional level and scope of the explosive gas environment is determined, such as within the scope of a region must use flame-proof lamps; 2 fixed lamps in the region can be explosion-proof and increased safety, mobile lighting must Flameproof type. The level or group of explosion-proof lights selected should not be lower than the explosive mixture level and group in explosion hazardous environments. At the same time, the impact of the environment on explosion-proof lamps should be taken into consideration, and the requirements of various environments such as ambient temperature, air humidity, corrosion, or contaminating substances should be met. According to different environmental requirements, the lighting protection level and corrosion protection level should be selected. Especially in the presence of corrosive gases in explosive gas atmospheres, it is crucial to select lamps with corresponding corrosion resistance.
In the past, among the petrochemical enterprises, the lighting fixtures in explosion hazardous locations were mainly flameproof. With the increasing use of increased safety electrical equipment in explosion hazardous locations in Zone 2, increased safety and composite lighting fixtures are also being used more and more. The increased safety type luminaire has the advantages of light weight, low price, convenient installation and maintenance, long service life, etc. compared with the flameproof type lamps on the basis of certain explosion-proof performance. The most widely used composite electrical equipment used in petrochemical enterprises is the Zengan-explosion-proof compound type explosion-proof electrical equipment. It is generally composed of three parts: explosion-proof parts, increased safety terminal blocks and increased safety enclosures. It has both flameproof safety. Performance, but also has the advantage of increased safety.
Sixth, install
Explosion-proof lamps must be checked from the nameplate and the product specification before installation: explosion-proof type, type, grade, group; degree of protection of the enclosure; installation method and fastener requirements for installation. The installation of explosion-proof lights must be securely secured, the fastening bolts must not be replaced, and the spring washers should be complete. The dust-proof and waterproof seals should be placed as they are. When the cable enters the line, the cable and the sealing gasket should be closely matched. The section of the cable should be round, and the surface of the jacket should not have defects such as asperities. Extra inlets shall be sealed in accordance with the type of explosion protection, and tighten the compression nut to seal the inlet.
Seven, maintenance and repair
1, routine maintenance
In routine maintenance, the following points need to be noted.
(1) Explosion-proof lights and lampshades shall be able to automatically cut off the power before they are opened. However, because the interlocking devices are relatively complex and difficult to implement, most of the lamps and lanterns are only equipped with warning signs such as “No Live-On†on the housing. Because of the high surface temperature after the power failure of the lamp, if you open the NSC9720A tunnel lamp immediately, there is still the danger of igniting explosive gas mixtures (mainly flameproof structures). Therefore, the bulb surfaces of incandescent lamps, high-pressure mercury lamps, and high-pressure sodium lamps A high-temperature light source can quickly open the cover of the luminaire and pay attention to this point. The use of more CeY-1 explosion-proof fluorescent lamps by the company's unit has an interlock mechanism that opens and closes the power supply, providing convenience and safety for maintenance work. Because the fluorescent lamp is a cold light source lamp, there is no surface high temperature, and the lid can be opened immediately after the power is turned off.
(2) In the replacement of light bulbs (tubes), the flameproof joints of explosion-proof lamps shall be properly protected and shall not be damaged; the flameproof surfaces after cleaning shall be coated with phosphated plaster or 204-1 anti-rust oil; Paint; flameproof surface may not have a rust layer, if there is a slight rust, after washing should be no hemp surface phenomenon. The seals used for dust protection and waterproofing must be kept intact. This is very important for the increased safety lighting. If the seal is seriously damaged, replace it with a seal of the same size and material and replace the entire light if necessary. When overhauling, pay attention to whether the lampshade is intact and replace it immediately if it is broken.
2, regular maintenance
(1) Maintenance personnel need to be trained on the job to understand the performance of the lamps and use requirements clearly. Maintenance personnel must have professional knowledge and be familiar with the structure of the lighting products.
(2) Eliminating dust and dirt on the explosion-proof lamp housing regularly to improve the light efficiency and heat dissipation performance of the lamp. The cleaning method can be based on the protection capability of the lamp housing, using water spray (over the shade on the lamp) or using a damp cloth. When cleaning with water spray, the power should be cut off. Never use a dry cloth to scrub the plastic housing (transparent part) of the lamp to prevent static electricity.
(3) Check whether the plastic housing (transparent parts) of the lamp has serious discoloration, such as severe discoloration, indicating that the plastic has deteriorated. Check whether the transparent parts have been affected by foreign material, whether the protection net has loosened, soldered, and corroded. If so, use should be stopped and repaired and replaced in time.
(4) Light source damage should be turned off in time to inform the replacement, so as to avoid the ballast and other electrical components being in an abnormal state for a long time because the light source cannot be started.
(5) If there is accumulated water in the cavity of the lamp used in the humid environment, it shall be promptly removed, and the sealing parts shall be replaced to ensure the protective performance of the enclosure.
(6) When opening the lamp cover, press the warning sign and open the cover after turning off the power.
(7) After opening the cover, check whether the explosion-proof joint surface is intact, whether the rubber seal is hardened or sticky, whether the wire insulation layer is green and carbonized, and whether the insulation and electrical components are deformed and burnt. If these problems are found, they should be promptly repaired and replaced.
(8) The type, size, size, and performance of the replaced light source, parts, and electrical components shall be the same as those of the light source, components, and electrical components prior to maintenance and replacement.
(9) Before applying the cover, apply a damp cloth (not too wet) to lightly return the light and transparent parts of the lamp to increase the luminous efficiency of the lamp. A layer of 204-1 displacement rust preventive oil should be applied thinly on the flameproof joint surface. When the lid is closed, attention should be paid to whether the sealing ring plays a sealing role in the original position.
(10) The sealed part of the lamp should not be frequently disassembled and opened.
Â
VIII. Precautions
1, note
Portable luminaires are divided into two types: feed-grid-powered and self-powered. For lamps powered by the feed-in network, rubber-sleeved cables shall be used between the explosion-proof junction boxes (boxes) or explosion-proof plugs and the lamps. The grounding or connection of the neutral conductors shall be within the same jacket; the cable shall adopt the minimum allowable section of the main conductor core. 25 mm2 YC, YCW heavy duty rubber cable. One point to be emphasized here: The cable for portable lighting does not allow intermediate connectors.
The author's unit has had such an accident: one night to repair the pump, then the temporary explosion-proof lights, explosion-proof signs for the dIICT4. When the fitter picks up the lamp closer to the pump body, it ignites the gas leaking from the pump body and burns the face of one of them. After checking the explosion-proof performance of the lamp is normal, the problem lies in the lamp's cable. In fact, there is a cable joint at a distance of 15m from the lamp, which is wrapped with an insulating wrap. When the cable is connected to the lamp, the cable is dragged on the ground to expose the cable core. When the fitter lifts the lamp to illuminate the pump body, the core hits the channel of the equipment foundation. , igniting the ground and igniting the mixed gas. This accident exposed the loopholes in our explosion-proof safety management. After the accident, we carried out a thorough inspection of all portable lamps and their cables to eliminate the hidden dangers of similar accidents. This accident tells us that in the management of explosion-proof electrical safety, there must be no luck mentality. We must do it in strict accordance with relevant regulations and requirements in order to be foolproof.
(1) Flameproof electrical equipment
The electrical equipment of the enclosure of an electrical device with an explosive pressure capable of withstanding the explosive gas mixture of internal explosives and preventing the internal explosion from propagating to the explosive mixture around the enclosure is marked with “dâ€.
(2) Increased Safety Electrical Equipment
Under normal operating conditions no arcs, sparks, or high temperatures that may ignite the explosive mixture are structurally actuated to increase safety margins to avoid arcing, sparks, or high-humidity electrical equipment under normal and recognized overload conditions. Is "e".
(3) Explosion protection principle
There are two reasons for igniting flammable gas mixtures in electrical equipment: one is sparks, arcs generated by electrical equipment, and the other is heating of electrical equipment surfaces (ie, surfaces in contact with flammable gas mixtures). For components that can generate arcs and sparks during normal operation, they can be placed in flameproof enclosures, or other explosion-proof types such as encapsulated, sand-filled, oil-filled, or positive-pressure types can be used to achieve explosion-proof purposes. For the safety-enhanced electrical equipment, it is a device that will not generate arcs, sparks, and dangerous high temperatures during normal operation. If some protection measures are taken in its structure, it will try its best not to make the equipment under normal operation or under an approved overload condition. Arc, spark, and overheating can further increase the safety and reliability of the equipment. The NSC9720A rail tunnel light therefore has no ignition source in normal operation and can be used in explosion hazardous environments.
(4) Examples of Explosion-proof Marks
4.1 If the electrical equipment is Class IIB flameproof T3, the mark is ExdIIBT3.
4.2. If the electrical equipment is of type II increased safety, the temperature group is T2 group and the symbol is ExeIIT2.
4.3. If more than one type of electrical equipment is used, the main type of explosion protection shall be marked first, followed by other types of explosion protection. For example, the main body shall use increased safety type IIC flameproof components, the temperature group shall be T4, and the symbol shall be ExedIICT4. .
4.4 If the electrical equipment is dust explosion-proof and dustproof T11 group. The sign is: DIPDPT11.
2. Description
Explosion-proof lighting is a kind of lighting fixture with explosion-proof performance, with the sign of Ex. The sealing performance of explosion-proof lamps and lanterns, take further protective measures on the structure, etc., the state has certain requirements for explosion-proof lamps. Non-explosion-proof lamps do not have more than one requirement.
The first, explosion-proof lamps and lanterns explosion-proof categories, levels and temperature groups see the provisions of national standards.
Second, according to the type of protection against electric shock can be divided into I, II, III categories. The protection against electric shock is to prevent the explosion-proof lamp housing from being easily touched and the parts are electrified, so that the human body is exposed to electric shock or conductors with different potentials to generate electric sparks and ignite the explosive mixture.
AI class—On the basis of basic insulation, accessible conductive parts that are not energized during normal operation are connected to the protective ground conductor in the fixed line.
Class BII - Use double insulation or reinforced insulation as a safety measure without grounding protection.
Class CIII - Use a safe voltage with an effective value of not more than 50V, and no voltage above it will be generated.
Category D0 - only rely on basic insulation as a safety protection measure.
1 Ton Mini Excavator
1 Ton Mini Excavator XN10 have Koop engine ,Changchai engine and Briggs & Stratton engine,can be meet different market requirements.
Changchai :7.5kw - Stage III
Koop :7.6kw -Stage III
Koop :7kw -Euro V
Briggs & Stratton:13hp -EPA III
Rhinoceros brand mini excavator can be say Chinese 1 ton mini excavator originator,first manufacturer,the 1 ton mini excavator have been exported more than 5 years,the excavators also keep upgrad for meet customers's new needs.
The 1 ton mini excavator XN10 every years more than 2000 units mini excavators sell in Europe market,1000units sell in Australia market,more than 500 units to US ,Canada market.
Here are the newest design for 1 ton mini excavator XN10:
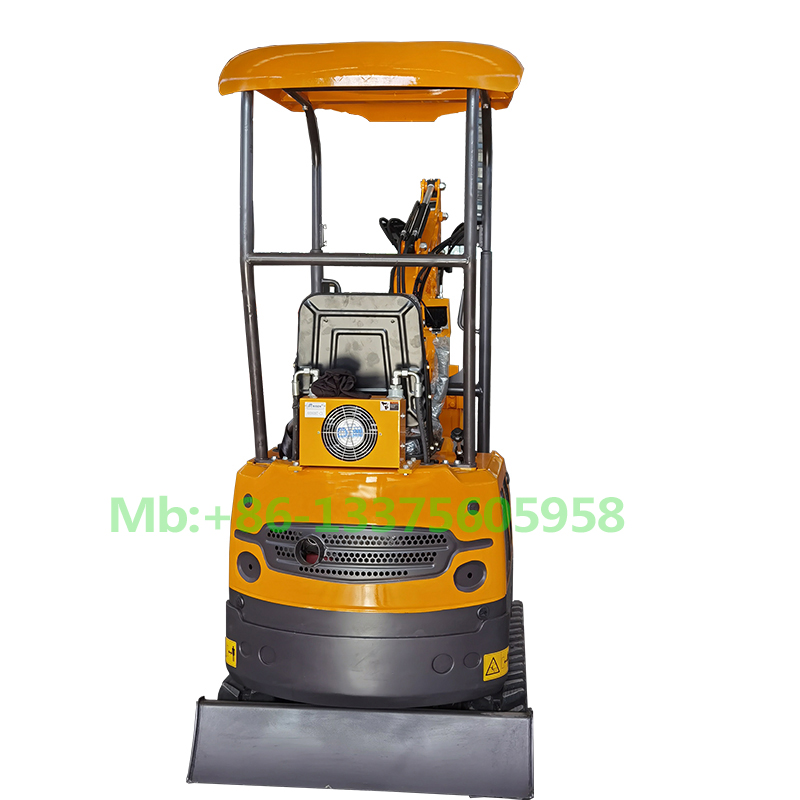
1 Ton Mini Excavator Machine,Mini Excavator 1 Ton,1 Ton Small Excavator,1 Ton Micro Excavator
SHANDONG KEN STONE HEAVY MACHINERY CO.,LTD , https://www.chinaexcavator.com