In order to further implement the deployment of the “Great Second Engineering†and “Quality Responsibility System†arrangements of CNHTC Group, CNHTC Jining’s final assembly plant will adopt the “Twelfth Five-Year Plan†target and the 2011 quality indicators to adopt “3:1 "Line" (ie: "check the problem with the target, according to the deep analysis of the problem, comprehensive analysis to find ways") work methods, so that the quality of Haoyun vehicle assembly has greatly improved. Around the "Three Points and One Line," the heavy truck Jining General Assembly Plant mainly carried out the following six tasks, and made active explorations for lean management and quality improvement, laying a solid foundation.
First, we must focus on the indicators of the number of failures in the downline and take measures to achieve initial success. The statistics of off-line faults directly reflect the quantity of quality problems that occurred on the day of production. After the vehicles went offline, sampling inspections were conducted before the vehicles were not commissioned, aiming to control the quality status of production line products. In 2011, CNHTC Jining Company demanded that the number of assembly factory quality indicators be controlled within 20 units. The assembly plant seriously carried out this work, increased inspections of large-scale lines, and counted the number of down-line failures after work every day. The data was then transmitted to the malfunctioning team. Each team leader then implemented it on the morning of the second day. Responsible person, do a rigorous assessment of the failure caused by personal assembly reasons. For the fault-prone work station, a key control point for assembly plant production was established and key control points were managed. Through the formulation and implementation of the above measures, the number of failures is basically controlled within 9 areas, which improves the quality level of the vehicle assembly process.
Second, attach importance to the passing rate of one inspection and improve the quality of the whole trains shipped by Haoyun. In order to meet the targets of off-line vehicles, the Jining General Assembly Plant of Heavy Duty Trucks has established and improved various management and assessment systems for quality problems that are easily encountered. Quality issues; adhere to the daily pre-class meeting to inform quality issues; the final assembly plant and the relevant person-in-charge at the same time talk to employees who are prone to quality problems, understand the real causes of the problems, and help employees find solutions to the problems; Everyone worked together. At present, the pass rate for the inspection of the assembly plant of CNHTC Jining has basically been raised to 80%. In the future, the Jining assembly plant will increase its efforts to innovate work methods and methods, strictly control the warehousing pass, increase the passing rate of one inspection, and continuously improve the quality of Haoyun's entire vehicle assembly.
Third, improve the process to further improve the quality of Haoyun's vehicle assembly. In the earlier period, due to the rapidity of vehicle model improvement and replacement, some vehicle models were still not perfect enough, and some workers had to rely on experience to load vehicles. As a result, the stations were not assembled according to the process in the past, leaving hidden dangers for improving the quality level of the entire vehicle. In order to improve the quality of Haoyun's vehicle assembly, the heavy truck Jining assembly plant has been deeply analyzed, carefully arranged, and seriously implemented. The joint technical department and quality department make process cards, carry out key training for each shift group and key positions, and rigorously assemble according to the process; the organization technical department, quality department, and related personnel form a process inspection and improvement team and conduct weekly training for each team. Inspection and improvement, found problems, timely rectification. This work is progressing from the assembly class to the second class and the third class. After a period of hard work, the effect is more obvious, which lays a good foundation for the standardization control and the improvement of the overall vehicle quality level.
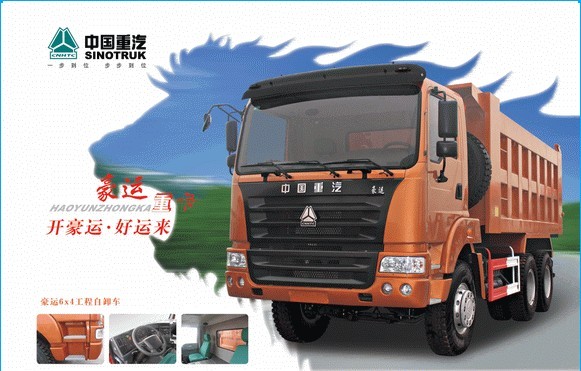
Fourth, we must start a weekly quality improvement meeting to ensure that all quality improvement systems and measures are implemented. CNHTC Jining General Assembly Factory held a weekly internal quality management meeting for the joint product development department, technical department, quality department, and production team leaders. He exchanged and communicated on the assembly and adjustment problems, parts quality issues, process and design development issues involved in the previous week, and sent out rectification opinions and completion time. At the meeting, everyone communicated and demonstrated issues that emerged, and actively sought the best ways and means of solving the problem. Through the quality regular meeting, an interactive platform was established between the team and the department, which was conducive to the rectification and implementation of the problem and to improving the vehicle. The quality of assembly has played a positive role in promoting.
Fifth, set up quality kanbans and strengthen awareness of quality management. Heavy truck Jining company assembly factory set up quality kanban in each team, kanban mainly announced the quality problems in the team, notice of quality improvement, assessment of staff assessment and rewards, quality improvement knowledge and so on. Through quality kanbans, the quality information is transmitted to each team and the grassroots assembly personnel in a more visual manner. A good atmosphere of competition and improvement is created between the team and the team. The effect on the improvement of the assembly quality of the whole vehicle is obvious.
Sixth, do a good job in quality management records and conduct quality assessment activities. A strict quality assessment system has been established within the CNHTC General Assembly Plant. The office of the assembly factory is responsible for the statistics of the quality problems that occur within the team and carries out quality assessment activities on a monthly, quarterly and annual basis. According to the performance of employees, quality improvement stars, quality improvement stars, best assembly stars and so on were established. The staff's assembly quality level is directly linked with the employee's star rating, employee performance salary, and promotion of officers. Through quality assessment activities, a good atmosphere of quality improvement has been created within the assembly plant, and the quality improvement has been implemented to the production line and the grassroots level. This has fully mobilized the enthusiasm of the front-line staff to participate in the quality improvement and has greatly promoted the Haoyun heavy truck. Improve the quality of assembly.
China National Heavy Duty Truck Group Jining Commercial Vehicle Co., Ltd. assembly plant "three points and one line" work method directly implemented in the above six measures from beginning to end, from the problem to the analysis of the reasons to solve and enhance, clear thinking, clear goals, measures properly, the effect Significant. We believe that the quality of Haoyun heavy-duty vehicle assembly will continue to increase, and will be further favored in the market. CNHTC Jining Commercial Vehicle Company will certainly seize the opportunity to achieve a new take-off and welcome new glories.
Cnc Machining,Cnc Lathe Machining Parts,Cnc Large-Scale Machining,Non-Standard Cnc Machining
Shenzhen Kairui Precision Technology Co., Ltd. , https://www.krcncmachine.com