Under a given operating condition, to adjust the cooling capacity of the system, it is necessary to change or. For refrigeration systems with fixed speed and fixed volume compressors, if the influence of the gas transmission coefficient is neglected, the actual gas delivery volume of the compressor is determined only by the structural parameters and rotational speed of the compressor, and the type and working conditions of the refrigerant. It has nothing to do with it and cannot be changed. For pure working fluids, there is nothing to do with changing the working fluid; however, for mixed working fluids composed of two or more boiling points of different pure qualities, the change is achievable. In general, a working fluid with a high boiling point has a low cooling capacity per unit volume, while a working fluid with a low boiling point has a high cooling capacity per unit volume; when the two are combined in different ratios, the mixed working fluid The unit volume cooling capacity can be varied within a wide range to achieve the purpose of compressor capacity adjustment.
According to the gas-liquid equilibrium theory of the mixture, there are some differences between the two components in the gas phase and the liquid phase under the same pressure and saturation state. The percentage of the low-boiling component in the gas phase is greater than that in the liquid phase. The percentage in the high boiling component is lower in the gas phase than in the liquid phase. Therefore, it is possible to select non-azeotropic mixed working fluids with similar thermodynamic properties and suitable components to form a large difference in temperature at the bubble point, and then separate and recombine the mixture by a specific device, thereby achieving a purposeful change of system circulation. The compositional concentration of the mass reaches the purpose of adjusting the system load. The development status of the variable concentration capacity adjustment device is roughly divided according to the position of the variable capacity device in the system, and the above-mentioned device is improved by You Ying et al.
The main purpose is to change the external heating source in the two liquid storage tanks to use high-pressure superheated gas to make the device more energy-saving. However, by using the effect of gas-liquid separation in the liquid storage tank to change the concentration of the system, the effect will be insignificant, and the magnitude of the concentration change is limited by the size of the liquid storage tank and the amount of the solution in the liquid storage tank, and it is difficult to achieve the desired capacity adjustment. effect. Therefore, he proposed that the two devices are only ideas and have not been implemented.
The component separation system is installed between the indoor unit and the throttle valve. Since the component separation system is disposed on the high pressure side of the system, it is not necessary to perform special insulation. The liquid storage tank in the separation system stores the volatile components separated by the rectification column, and solves the oil return problem of the system. In order to avoid excessively high compressor exhaust temperature when the volatile components in the system increase, a throttling valve is installed between the condenser outlet and the compressor inlet. The experiment proves that the compressor discharge temperature can be effectively prevented.
The main characteristic of such a device between the condenser and the evaporator is that the change of the working condition is used to change the opening degree of the expansion valve, so that the circulation flow rate of the system changes, thereby achieving the purpose of changing the components of the system. position.
The variable concentration device is mainly similar to the one in the condenser between the condenser and the compressor. The composition ratio of the mixed working fluid is changed by the change of the system flow rate of the mixed working fluid variable concentration capacity adjusting device. The only difference is that the two capillaries connecting the variable concentration system to the refrigeration system are not on either side of the expansion valve, but between the condenser outlet and the compressor suction port.
The main characteristic of such a variable concentration device between the evaporator and the compressor is that the outlet of the evaporator has a liquid working fluid outflow, and then the composition of the mixed working medium is changed by some variable concentration device to change the compressor. Inhalation specific volume, to achieve the purpose of system capacity change. Variable concentration device position.
Conclusions and Prospects According to the placement position of the variable concentration device in the system, several types of variable concentration capacity adjustment devices existing in the literature are summarized and the following conclusions are drawn: 1) The types of variable concentration capacity adjustment devices mainly have storage. The liquid tank, gas-liquid separator and rectification column are different from the separation effect of the high and low components of the mixed working fluid, and the effect of separating and changing the concentration by the rectifying column is better than that of the liquid storage tank and the gas-liquid separator.
2) In order for the variable concentration adjusting device to function, it is necessary to have a mixed working medium mainly composed of liquid or liquid to flow into the variable concentration adjusting device. Therefore, the inlet end of the variable concentration device must be placed in a place where the liquid working medium flows out (eg At the condenser outlet or at the evaporator inlet, the actual effect of changing the composition is better than at a location where there is no liquid working fluid or liquid working medium (eg compressor outlet or evaporator outlet).
Cutting Oil:
Cutting fluid by a variety of super functional additives through scientific composite fit, and has good cooling performance, lubricating performance, rust resistance, oil removal the function of cleaning, corrosion, easy dilution characteristics. To overcome the traditional soap emulsion summer winter easy smelly, difficult dilution, anti rust effect difference problem, and has no adverse effects on the lathe for black metal paint, cutting and grinding, grinding is the current most. Leading indicators are better than the saponification of cutting fluid it has good oil, cooling, cleaning, rust and other characteristics, and has non-toxic, tasteless, no corrosion on the human body, the equipment corrosion, the characteristics of environment pollution.
Category:
The cutting fluid can be divided into straight oil,water-based emulsion, or soluble oil,semisynthetic cutting fluid and synthetic cutting fluid. The emulsion, semi synthetic and synthetic classification usually depends on the basis of oil products in the category: the emulsion is only with mineral oil as base oil soluble cutting fluid; semisynthetic cutting fluid containing both mineral oil and base oil containing chemical synthesis of water-soluble cutting fluid; synthetic cutting fluid is only the use of chemical synthetic base oil (which does not contain mineral oil) water soluble cutting fluid. The cutting fluid of each type will contain a variety of additives in base oil outside: anti rust agent, nonferrous metal passivation of corrosion agent, defoaming agent and so on. Some manufacturers will have a classification of micro emulsion; usually considered between emulsion and semi synthetic cutting fluid categories. Diluted emulsion is milky white in appearance; dilution semi synthetic fluid is usually translucent Some products are milky white; the dilution of the synthetic solution is usually completely transparent, such as water or a certain color.
Function:
Lubrication of metal cutting fluid (the cutting fluid lubrication) in the cutting process, can reduce the rake face and chip, flank and inter surface friction, forming part of lubricating film, thereby reducing the cutting force, friction and power consumption, reduce the temperature of the wear surface and the cutting tool and the workpiece blank the friction parts, improve the cutting performance of the workpiece material. During the grinding process, adding grinding fluid, grinding workpiece and the lubricating film formed between the abrasive and grinding fluid into the grinding wheel, the friction interface decreases, prevent the abrasive cutting edge wear and adhesion of the chip, thereby reducing the grinding force and friction heat, improve the durability of the grinding wheel and the workpiece surface quality.
The cooling effect of cooling liquid is cutting through it and by cutting a heating tool (or wheel), chip and workpiece between convection and evaporation, the cutting heat from tooling A place away, thus effectively reducing the cutting temperature, reduce the deformation of the workpiece and the cutting tool heat, keep tool hardness, improve the machining accuracy and tool durability. The cooling performance of cutting fluid and its thermal conductivity, specific heat, heat of vaporization and viscosity (or liquidity). The thermal conductivity and heat capacity of water is higher than that of oil therefore, the cooling performance of water is better than cleaning oil. During the metal cutting process, cutting fluid has good effect of cleaning requirements. To remove debris and produce chips, iron, oil and sand, prevent the machine tool and the workpiece, the tool of contamination, so that the cutting edges of the tool or grinding mouth to keep sharp, does not affect the cutting the effect for oil based Cutting Oil, lower viscosity, cleaning ability is stronger, especially with kerosene, diesel oil cutting and other light components, permeability and cleaning performance better. Water-based cutting fluid containing surfactant, the cleaning effect is better, because It can form film on the surface, to prevent the sludgeparticles and adhesion in the workpiece, cutting tool and grinding wheel, at the same time it can seep into the sludgeparticles and adhesion of the interface, it separated from the interface with the cutting fluid, cleaning rust away, keep the interface.
In the process of metal cutting work and environmental media and cutting fluid component decomposition or oxidation and sludge produced with the corrosive medium and corrosion, the surface of machine parts in contact with the cutting fluid will be corrosion. In addition, between the workpiece or the process of the transfer process also requires temporary storage, cutting fluid has certain anti rust capability, to prevent environmental media the residual sludge in cutting fluid and other corrosive substances to cause erosion of metals. Especially in the south of our country, humid and rainy season, more attention should be paid to rust.
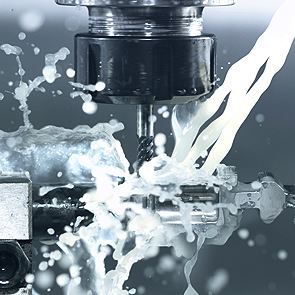
Cutting Oil
Cutting Oil,Soluble Oils,Semisynthetic Fluids,Synthetic Fluids
VESTA Motoring Ltd , http://www.vesta-industry.com