Second, mineral filler and surface modification process
(a) calcium carbonate
Calcium carbonate is currently the most widely used inorganic filler, and according to statistics, it accounts for about 70% in the plastics industry. The advantages are wide source, low price and no toxicity. Calcium carbonate has two kinds of light calcium carbonate and heavy calcium carbonate. Calcium carbonate which has not been surface-treated generally has poor affinity with organic polymers, and is liable to cause uneven dispersion in the polymer binder to cause interface defects of the two materials. These disadvantages become more pronounced as the amount of filling increases. Therefore, in order to improve the filling property and acid resistance of calcium carbonate, it is subjected to surface modification treatment. For light calcium carbonate, the modification can be accomplished simultaneously in the calcium carbonate preparation process.
The surface modification method is mainly calcium carbonate coating chemical modification, surface modifying agents include fatty acids (salts), titanate coupling agent, a zirconium aluminate coupling agent and a polyolefin oligomer.
1. Stearic acid (salt) treatment The stearic acid (salt) treatment is the most commonly used surface modification method for calcium carbonate fillers. Generally, calcium carbonate is first dried to remove moisture, and then it is carried out in a high speed kneading (or mixing) machine. The drying temperature is controlled at 100~110 °C for 0.5~1.0h, depending on the water content of calcium carbonate. The stearic acid is then added directly to the high speed kneader. The amount of stearic acid is generally 0.8% to 1.0% of the amount of calcium carbonate added, and the reaction temperature is controlled at about 100 °C. In the kneading (or mixing) machine, stir vigorously for 15~30min at high speed, and then discharge the package.
The trade name of light calcium carbonate after treatment with stearic acid is activated calcium carbonate or white Yanhua. Compared with calcium carbonate which has not been surface-modified, Bai Yanhua can improve the rheological properties of polymer-based composites, and the physical properties and mechanical properties are also improved.
Except that stearic acid (salt), other fatty acid salts or esters, such as phosphate salts and the like can also be used for surface modification treatment of calcium carbonate. It has been reported that the surface treatment of light calcium carbonate by using stearic acid and sodium dodecylbenzenesulfonate can improve the surface modification effect. The ratio of stearic acid to sodium dodecylbenzene sulfonate is 2:1, and the amount is 2.5% to 3% and 1.25% to 1.5% of the amount of calcium carbonate, respectively, and the reaction temperature is 90 °C.
The modified calcium carbonate treated with stearic acid (salt) is mainly used for filling polyvinyl chloride plastics, cable materials, adhesives, inks, paints, and the like. It can also partially replace carbon black, white carbon black reinforcing filler and titanium dioxide.
2. Titanate modifiers Compared with stearic acid and salts, calcium carbonate is treated with titanate, and its product properties can be further improved, not only with polymer molecules, but also with titanic acid. The ester can form a molecular bridge between the calcium carbonate molecule and the polymer molecule, which increases the interaction between the organic high polymer or the resin and the calcium carbonate, thereby correspondingly improving the mechanical properties of the composite material, such as impact strength and stretching. Strength, bending strength, elongation, etc.
Figure 3 Process flow chart of calcium carbonate composite coupling system
Figure 3 is a process flow diagram of a calcium carbonate composite coupling system. The composite system is a process for comprehensively treating (modifying) the surface of calcium carbonate particles based on a titanate coupling agent in combination with other surface treatment agents, crosslinking agents and processing modifiers. The surface treatment agent is stearic acid, and the calcium carbonate is treated with stearic acid alone, and the effect is not satisfactory. When stearic acid is mixed with the titanate coupling agent, a good synergistic effect can be obtained. The addition of stearic acid does not substantially affect the coupling of the titanate, and at the same time, the amount of the coupling agent can be reduced, thereby reducing the production cost. The cross-linking agent bismaleimide allows the inorganic filler to be more tightly bonded to the matrix resin by cross-linking technology, further improving the mechanical properties of the composite material, which is Bai Yanhua or simple titanate surface modification. Handling is difficult to achieve. The surface modifier is various polymer compounds such as 80-resin. Its addition can significantly improve the melt flow properties of the resin, the thermal deformation properties and the gloss of the surface of the product. In order to coat all the surface of the calcium carbonate particles with a coupling agent molecule, it can be modified by spraying or dropping as a method of emulsion impregnation, and then filtered, dried, pulverized and kneaded with a crosslinking agent and the like at a high speed. (or mixed), evenly dispersed. The calcium carbonate after the composite coupling treatment is a white powder with a density of 2.7-2.8 g/cm3 and a pH of 7-8, and the hydrophobic property is good. [next]
For the same inorganic fillers and pigments, different modifiers are used, and the filling effect is also different. The appropriate surface modifier should be selected to optimize the use.
(2) Kaolin
Kaolin is a layered silicate mineral with a hydroxyl group and an oxygen-containing group on the surface, which is acidic; the calcined kaolin is more acidic, so it needs to be surface-modified when used as a filler. After the surface of the kaolin particles is modified, it can achieve the purpose of waterproofing, reducing surface energy, improving dispersibility and improving the performance of plastics, rubber and other products. The modified kaolin is mainly used for reinforcing materials of nylon, compatible fillers in polar polymers such as polyurethane and polyester, rubber fillers and fillers of electrical insulating materials. The types of surface modifiers used vary depending on the kaolin use. There are mainly silanes, silicones (silicone oils), titanates, stearates and cationic surfactants. The treatment process is relatively simple, and the mineral and the prepared medicament are generally added together in a high-speed mixer. The surface properties, particle size, type and amount of modifier, surface treatment time and temperature of the treated kaolin are the main factors affecting the modification effect.
1. Treatment with Silane Silane is the most commonly used and most effective surface modifier for the treatment of acid kaolin fillers. Different uses, different application requirements for kaolin, so the type of silane selected is also different, and the dosage must be appropriate. Excessive dosage may lead to multi-layer coating, which is not only unnecessary, but also increases the processing cost. The general dosage is 0.5% to 3.0%. The optimum amount is determined experimentally according to the particle size, specific surface area and surface characteristics of the material to be treated.
The calcined kaolin used for the high-voltage cable insulation filler not only has to improve the mechanical strength of the material, but also has high electrical insulation, and the electrical insulation does not decrease in a humid environment, which requires not only the selection of silane but also the silane. Considering its hydrophobicity, that is, poor permeability after coating on the surface of kaolin, and higher volume resistivity or lower dielectric constant, it is usually treated with silicone oil. The test shows that when the surface of the calcined kaolin powder is treated with domestically produced 202, 256, 1, 3, and 6 silicone oils, the amount of silicone oil and the treatment time increase under the same conditions, and the hydrophobicity of the kaolin becomes better. Too much excess will increase the cost, so the general dosage does not exceed 3% of the filler.
The kaolin filler is used in the rubber, and the silane for surface modification can be selected according to the vulcanization mechanism of the rubber. When using a peroxide catalyst, with a vinyl silane (or unsaturation); and when using the sulfur or metal oxide as a catalyst, the mercaptans should be used, or an amino silane.
The finer the particle size of kaolin, the larger the specific surface area, and the more exposed hydroxyl groups. The amount of surface modifier required to achieve the same coverage is undoubtedly greater than that of coarse-grained kaolin. In addition, the finer the particle size, the better the overall application performance. The results of the use of vinyl silane modified different particle size calcined kaolin for EPDM fillers indicate that the final product has tensile strength, 300% modulus, tear strength and electrical insulation properties. The kaolin filler is significantly better than the medium particle size calcined kaolin filler.
Studies by the British Clay Company have shown that the morphology of the silane adsorbed or reacted on the clay surface depends on the concentration of hydroxyl groups on the surface. Where the surface hydroxyl concentration is high, a two-dimensional thin layer like a silane layer is formed. If the hydroxyl concentration of the surface is low, the number of active points for the silane reaction is reduced, and a second bridging layer of silane molecules is formed; when at a critical concentration At the same time, the two layers of silane molecules further promote the bridging effect. The three-dimensional structure is more effective for improving the rubber reinforcement. Therefore, if the silane is adsorbed on the surface of the kaolin which has been heated to the dehydroxylation temperature (550 ° C), the treatment with silane will achieve a more remarkable effect. The silane-treated calcined (dehydroxylated) kaolin has higher hardness and modulus than the uncalcined kaolin, but its permanent deformability, tensile strength and shear strength are lower, and the difference may be off Caused by changes in the size of the kaolin during the hydroxylation process.
It has been reported that after amination (ammonia gas) treatment, silicate minerals such as aminated kaolin are surface-treated with oxalic acid, sebacic acid, dicarboxylic acid and the like. The modified kaolin treated by this method is used as a filler of nylon 66, and its performance is superior to that of 1% aminosilane-treated kaolin.
In addition, when silane coating treatment, proper addition of other surface modification (treatment) agents can not only reduce the amount of silane which is more expensive, reduce the cost, but also enhance the surface treatment effect. Within a certain range, higher processing temperatures can accelerate the chemical reaction of silane molecules with the kaolin surface. However, the optimum processing time and processing temperature of the material will vary depending on the silane. Therefore, after the silane is selected, it is preferable to determine the optimum treatment time and treatment temperature by experiment.
2. Cationic surfactant After the surface modification of kaolin with octadecylamine, the surface hydrophobicity can be enhanced, but the amount should not be too large. Surface treatment of kaolin powder with a quaternary ammonium salt polymer such as a polymer DADMAC of diallyldimethyl quaternary ammonium chloride can improve the application properties of kaolin in the coating.
(3) Wollastonite
Wollastonite is an inorganic acicular mineral widely used as a polymer base because of its non-toxicity, chemical corrosion resistance, thermal stability and dimensional stability, excellent mechanical and electrical properties, and reinforcing effects. Reinforcing filler for composite materials. However, the surface of natural wollastonite is hydrophilic and has poor compatibility with organic polymers, so the direct addition and dispersibility is not good, and it must be subjected to surface modification treatment to improve the compatibility with the polymer and enhance its reinforcing effect. The mechanical properties of the polymer-based composite filled with wollastonite powder are better. For example, when a wollastonite-filled polycarbonate treated with a silane modifier has a modulus of elasticity that is three times that of unfilled, the strength is increased by about 15%; filling into polyethylene improves its strength and electrical insulation properties. and superior talc and mica powder.
The treatment of wollastonite with a silane coupling agent can greatly improve its compatibility with the polymer and enhance the filling effect, but the silane coupling agent is more expensive. Therefore, under certain application conditions, the surface modification of wollastonite powder is carried out with cheaper common surfactants such as stearic acid (salt), quaternary ammonium salt, polyethylene glycol, fatty alcohol polyoxyethylene ether, and the like. Processing is more appropriate. These surfactants cover the surface of the particles by the action of polar groups and the surface of the particles, which greatly enhances the hydrophobicity of the wollastonite filler. [next]
Treated with stearic acid, when the amount is 1.0%, its coverage on the wollastonite surface can reach 77.43%, making the wollastonite surface change from hydrophilic to hydrophobic.
Wrapped wollastonite with polyethylene glycol (PEG) having a relative molecular mass of 2000-4000 can effectively improve the notched impact strength and low temperature performance of filled polypropylene (PP). Before use, the polyethylene glycol is dissolved in a certain amount of absolute ethanol to prepare a solution of a certain concentration. The wollastonite is treated with this solution and then filtered and dried. X-ray photoelectron spectroscopy (XPS) was used to determine the C/Ca data of wollastonite treated with different amounts of polyethylene glycol. The results showed that the C/Ca ratio of the wollastonite surface was 1.60, and the silicon was coated with 4% PEG. The C/Ca ratio of the limestone surface was 6.30, and the C/Ca ratio of the 4% PEG-coated wollastonite surface after 2000 ml of absolute ethanol and 2000 ml of 80 ° C hot water was 2.91. This indicates that a part of the PEG has been firmly coated on the surface of the wollastonite particles, that is, it is not peeled off by washing with a large amount of absolute ethanol and hot water. This layer of PEG coating has a great relationship to improve the notched impact strength and low temperature performance of filled PP. Studies have shown that under the same conditions, as the concentration of PEG solution increases, the amount of PEG coated on the surface of wollastonite particles also increases. When the amount of PEG accounts for 6% of wollastonite, the concentration of PEG is increased, and the PEG coated on the wollastonite surface is no longer increased, indicating that the coating has reached equilibrium. The relationship between treatment time and surface coating showed that after about 45 minutes, the coating of polyethylene glycol on the surface of wollastonite powder reached equilibrium.
The surface treatment of wollastonite powder with fatty alcohol polyoxyethylene ether type showed that the effect was also good. The mechanism of action of nonionic surfactants on the filling system is similar to that of various coupling agents. Hydrophilic groups and lipophilic groups interact with fillers and polymers, respectively, to strengthen the relationship between the two and improve the compatibility of the system. Sex and uniformity. The flexible carbon chain between the bipolar groups acts as a plasticizing lubricant, imparting toughness and fluidity to the system, reducing the viscosity of the system and improving processability.
Modified wollastonite treated with a combination of dodecyldimethylbenzylammonium chloride (DDB) and softener SG (condensate of stearic acid and ethylene oxide) can partially replace expensive Titanium dioxide is used in coatings. The treatment process is as follows: the wollastonite powder after weighing is put into the water-immersing tank, and the water is immersed for 24 hours according to the mass ratio of water: mineral powder=3:1, and the material after the water immersion is put into the reaction kettle to the mineral powder: hydrochloric acid (32% HCI) = 3.1:1 mass ratio of hydrochloric acid, then add 0.02% DDB and 0.5%~1% softener SG (addition amount is based on the quality of the ore powder); then warm to 70~80 °C, This temperature was kept stirring for 2 h. Finally filtered, washed with water (to remove residual materials CI -), drying, grinding.
(4) Mica minerals modified with surfactants as reinforcing fillers for polymer-based composite materials not only improve their strength, but also reduce mold shrinkage. Commonly used surface modifiers are silane, zirconium aluminate, and the like. Studies have shown that the mica used for surface modification is preferably wet-milled mica powder, and the most effective surface modifier is aminosilane. Mixing the two surface modifiers tends to be more effective, especially to greatly improve the mechanical and physical properties and aging resistance of the mica polypropylene composite. However, the optimum amount of modifier should be considered in consideration of the specific surface area of ​​the mica, the quality requirements of the product, and the processing cost. In addition, the variety of modifiers also affects the use of mica after surface treatment. The product grade LICA (a new alkoxy titanate) has a better modification effect on mica-filled PBT and PP. KR12 or KRTTS (monoalkoxy titanate) is not effective.
Modified mica reinforcing fillers are mainly used in polyolefins, polypropylene, polyethylene, polyamides and polyesters. Among them, polyolefin is the largest application area.
(5) Other mineral fillers Talc powder filled polypropylene has been widely used in the automotive industry and daily necessities, and has good apparent quality, low shrinkage and high heat distortion temperature compared with polypropylene without talc. However, due to the incompatibility of the two-phase interface, the filling of talc often leads to some deterioration in mechanics and processing properties. This limits the application of composite materials. Surface modification treatment can effectively improve the interfacial affinity of talc powder and polymer, improve the wetting ability of polymer to talc powder, improve the dispersion state of talc powder filler in polymer matrix, and thus improve The physical properties of the composite, such as impact strength.
Surface modifiers for talc are mainly various surfactants, titanates, zirconium aluminates and phosphates. The talc powder treated with silane can improve the various properties of the filler material ABS to varying degrees, especially the heat aging resistance. The performance study of the talc filler material treated with phosphate ester showed that the amount of phosphate ester had a great influence on the stretching and bending of the filled polypropylene. When the amount of the alkylphenol ethoxylate phosphate is 0.5%, the material exhibits the maximum tensile rupture strength and tensile yield strength. Continue to increase the amount, the intensity value will decrease, and will not change after 6%. The treatment process comprises the following steps: first pretreating the talc powder in an aqueous phosphate solution at 80 ° C for 1 h, then drying at about 95 ° C, and finally raising the temperature to 125 ° C, and heat-treating for 1 h.
In order to improve the compatibility of the surface of the silica and other forms of silica powder with the polymer, a surface treatment is carried out using a silane containing an organic functional group such as an amino group, an epoxy group, a methacryl group, a trimethyl group, a methyl group or a vinyl group. Since such powders may have functional groups such as Si—OH, Si—O—Si, Si—OH...O (surface adsorbed free water) in water and air, it is easy to accept functional groups in the above silane. However, since the hydrophobic group R of the silane is selective for a material such as a resin, the amount of the silane to be modified should be considered in consideration of the type of resin to be filled with the quartz powder, and the amount of the silane can be determined according to the specific surface area of ​​the quartz filler or by experiment. . There are two treatment processes, namely wet mixing and dry mixing. The wet mixing method is to forcibly mix and mix the treatment liquid with a suitable diluent and auxiliary agent and a silane modifier, soak the quartz powder, and then remove the water. This method is more complete, but the treatment cost is higher; while the dry mixing method is to add a small amount of diluent and silane to form a treatment agent, and the treatment agent is sprayed into the quartz powder at a certain temperature in a high-speed stirring mixer. After being stirred for a certain period of time, the material is discharged, and the method does not need to be dehydrated and dried, and the treatment cost is low.
The silane-modified silica powder is commonly used in epoxy plastics, high polymer based electrical materials, anticorrosive materials, and nuclear technology laboratory floor coatings. [next]
III. Evaluation of Surface Modification Effect The most reliable way to evaluate the surface modification effect of minerals is to conduct direct application tests to examine changes in product properties (such as tensile strength, impact strength, elongation, etc.). But this is a time-consuming and laborious task. Therefore, the physicochemical properties and surface properties of the modified materials are usually measured, and the changes of the indexes before and after the modification are compared to achieve the purpose of pre-evaluating the modification effect. The basic methods are as follows:
(1) Wettability
Modification of the mineral surface used as a filler or pigment, the most important is to make the original hydrophilic surface a hydrophobic surface. In principle, methods for measuring the wettability of solid surfaces, such as wetting equilibrium contact angle, wetting equilibrium height (climbing height method), wetting method, and determination of water vapor and gas adsorption amount, are applicable. However, it is more convenient and commonly used to measure changes in oil absorption rate or penetration rate and water absorption rate. The method for determining the oil absorption rate has been widely used in production.
(2) Dispersibility
The dispersion of particles in different media is one of the important indicators to characterize their performance. There are many methods for measuring dispersibility, and the usual methods are viscosity method and sedimentation method.
The viscosity method generally selects an organic liquid, and the powder to be inspected is added. After thorough stirring, the viscosity of the suspension is measured by a rotary viscometer at a constant temperature (usually 25 ° C). If the resulting viscosity value is low, the liquid is better able to wet the surface of the mineral.
The sedimentation method is to select one or several kinds of liquids, and to prepare the modified and unmodified powders into the same concentration of suspension, to carry out the sedimentation test, or to measure the downward moving speed of the clarified interface, or to fix from the same time. The position is extracted from a constant volume suspension to measure the concentration or to measure the volume change of the deposit to identify the modification effect of the mineral.
(3) Infrared spectroscopy (IR)
Infrared spectroscopy is an extremely important tool in the study of mineral surface modification. Because as long as there is a certain functional group or bond on the surface, there is a corresponding characteristic peak in the mineral spectrum. Therefore, the infrared spectrum analysis of the mineral samples subjected to various treatments before and after the modification and after the modification, according to the change of the corresponding characteristic peak, The role and mechanism of the surface modifier can be revealed.
(4) X-ray diffraction studies the structure of solid materials, X-ray diffraction is undoubtedly one of the most important methods. Polycrystalline samples can be used for crop phase identification and lattice parameter determination, and X-rays can be used for single crystals for structural and crystal integrity studies.
Some minerals such as montmorillonite, sepiolite, calcined kaolin, etc., after surface modification by modifier or mechanical chemical modification, not only change the surface properties of the mineral, but also its internal structure or crystal form. It changes. At this time, X-ray diffraction analysis is used to study the modification effect, and information can be obtained. The sodium removal Danjing Yang Jimeng ionic surfactant cetyl trimethyl ammonium bromide (of CTMAB) and cetylpyridinium (CPB) made after the modified adsorbent, to remove water, benzene, toluene, ethylbenzene and pollution The material was found to have a large increase in adsorption capacity. X-ray diffraction experiments show that the intercalation of organic ammonium leads to a widening of the interlayer spacing of the clay layer, and the adsorbed organic molecules enter the clay layer to further enlarge the interlayer distance. This result better illustrates the mechanism of action of the modified clay. .
(5) Thermal analysis of mineral surface modification products, a considerable part of which is used as rubber or paint (paint) fillers, all of which involve thermal stability of the modifier. Therefore, thermal analysis of the modified product is required. The point is also to get a lot of deeper information from it.
Thermal analysis mainly includes differential thermal (DTA) and thermogravimetric (TGA) analysis. Differential thermal analysis can be used to investigate the thermal effect of a material undergoing a phase change or some chemical reaction during heating. An exothermic or endothermic peak appears on the analytical curve. The size of the peak area reflects the thermal effect. Strength. Differential thermal analysis of minerals before and after modification, and comparison of the changes, can analyze the surface modification effect of minerals and its mechanism; thermogravimetric analysis can measure the change of mass of matter as a function of temperature or time. In the thermal analysis, by combining the above two thermal analysis methods, that is, while measuring the differential thermal curve, the thermogravimetric curve is recorded, and the temperature range in which the exothermic peak (or endothermic peak) appears on the differential thermal curve is just the heat. The temperature range of the thermal weight loss on the heavy curve. According to this, the total weight loss rate of the organic substance, the adsorption amount of the modifier, and its coverage on the mineral surface can be directly determined.
(VI) Surface analysis New technology Solid surface analysis technology is a high-tech developed in the past decade, such as electron energy spectrum, secondary ion mass spectrometry, etc., and its types are no less than dozens, but four or five kinds are widely used. The common basis of these techniques is that low-energy primary particles (photons, electrons, ions) interact with solid surfaces to produce discolored or emitted secondary particles. The relevant surface information can be obtained by analyzing the energy spectrum, mass spectrum or spectrum of the emitted particles. The measurement depth, parameters and characteristics of various common methods are shown in the table below.
Method name | Incident/out | Approximate measurement | Measurement parameter | Characteristics |
Shot particle | Depth/nm | |||
AES (Auger) electron spectroscopy | Electronics / Auger Electronics | 10 | Composition, ion valence | The most widely used, but the damage to the sample is large, especially for organic matter |
ISS (ion scattering spectrum) | Ion/ion | 0.3 | Composition, ion repositioning | Highest sensitivity |
ESD (electron or ultraviolet light induced desorption) | Electron or ultraviolet light/ion | 0.3 | Composition, key direction | It is actually a combination of SAM and SIMS, which can directly detect adsorbed specimens, and is a good method for studying adsorption. |
SAM (Scan Auger Electron Probe) | Electronics / Auger Electronics | 0.1~1 | Composition and valence | Not only get the spectrum, but also get an intuitive element map |
SIMS (Secondary Ion Mass Spectrometry, Ion Microprobe Mass Spectrometry) | Ion/ion | 5.0 | composition | High sensitivity, high resolution, trace analysis, complex mechanism, quantitative analysis of spectra |
XPS=ESCA (X-ray photoelectron spectroscopy) | X-ray/inner layer electron | >10.0 | Composition, valence state, charge analysis and structure of atoms in molecules | It has little effect on radiation damage of samples and is widely used. |
UPS (UV photoelectron spectroscopy) | Ultraviolet light/electron | 5.0 | Surface state, bond direction, ion valence | Similar to XPS |
It can be seen from the table that the application of these surface spectroscopy techniques can suggest many information such as the composition of the solid surface, the valence state of the ions, and the chemical bonds. A large number of facts show that the application of new techniques for surface analysis has unique advantages in deep theoretical research, suggesting modifiers and mineral surface action mechanisms. However, due to the complexity of the equipment and the high level of operation, these new technologies are still difficult to apply universally.
The design of middle through hole is easy to install, Barrel Damper is usually used in small spaces. ABD barrel dampers are the perfect solution for a wide range of applications. Barrel dampers are widely used in automobile interior decoration, household electric appliances, furniture, hidden socket, etc. Our dampers can make the movement of structures soft, quiet and safe to mitigate the impact, avoid the damage, increase the mechanical life, reduce noise, and improve product quality.
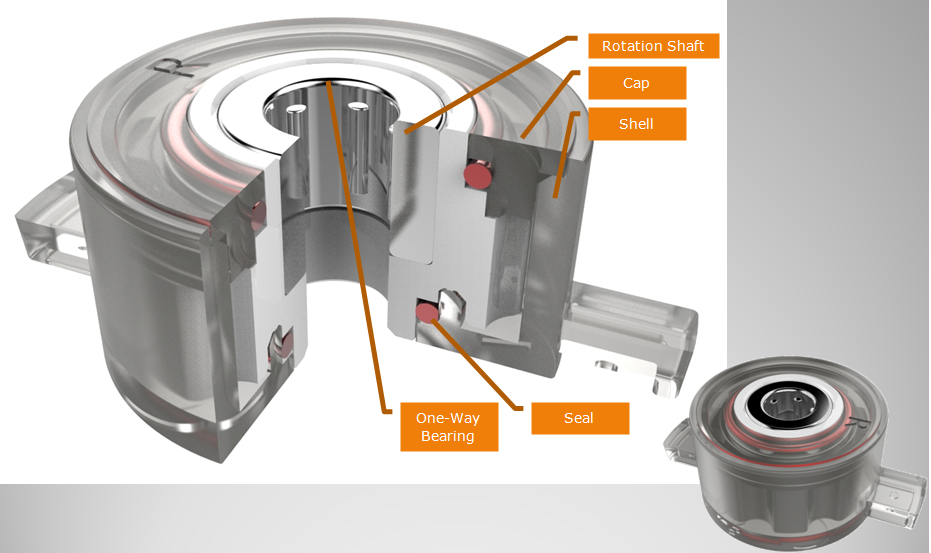
NOTE:
1. Please contact the corresponding product engineer for specific torque products.
2. Max. rotation speed: 50r/min
3. Max. circle rate: Clockwise180 °, 180 ° anti-clockwise for 1 cycle
4. Operating temperature: -10~50℃
5. Storage temperature:-30~60℃
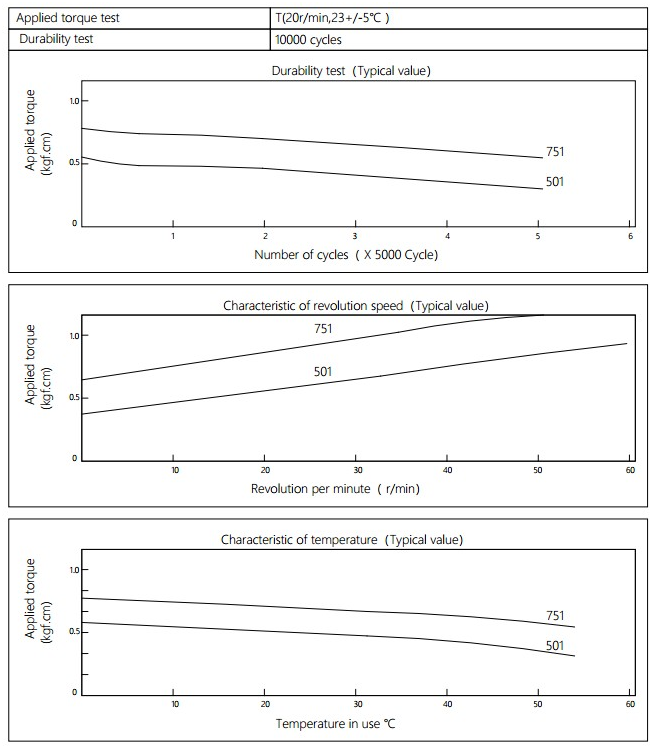
Applied torque:(T)
Test Temperature:23+/-5℃
Rotating speed:20r/min
Durability test Method:Clockwise 180 °, 180 ° anti-clockwise
Rotating speed:20r/min
Test Frequency:1cycle/min
Test Temperature:23±5℃
Durability test cycle:10000 cycle
Test result criteria: Store in the room temperature for 24 hours or more after the test, recording to the torque T=T±30%T.
Barrel Damper
Barrel Damper,Plastic Dampers,Manual Barrel Damper,Toilet Seat Damper,Plastic Barrel Rotary Damper
Shenzhen ABD Equipment Co., Ltd. , https://www.abddamper.com